PCB傳感器在工業自動化控制中的發展趨勢
點擊次數:14 更新日期:2025-07-23
PCB傳感器是一種將敏感元件與信號處理電路集成于PCB上的微型化傳感器,廣泛應用于工業自動化控制領域,用于測量物理量(如壓力、溫度、位移、加速度、振動等)并轉化為電信號,為設備狀態監測、過程控制及智能決策提供數據支撐。隨著工業4.0、智能制造的推進,PCB傳感器正朝著??高精度、集成化、智能化及網絡化??方向發展,其技術革新與市場應用呈現顯著趨勢。以下從??技術演進、功能拓展及行業應用??三方面展開系統性分析。
??一、PCB傳感器的技術發展趨勢??
??1. 微型化與高集成度??
傳統傳感器受限于分立元件設計,體積較大且布線復雜,難以滿足工業設備小型化、輕量化的需求。PCB傳感器通過將敏感元件(如MEMS芯片)、信號調理電路(如放大器、ADC)及通信接口直接集成于PCB板,顯著縮小了體積(如壓力傳感器尺寸從傳統Φ15 mm縮小至Φ5 mm),同時提升了集成度。
??MEMS技術融合??:微機電系統(MEMS)技術的成熟推動PCB傳感器向納米級精度發展。例如,MEMS加速度傳感器可檢測0.001 g的微小振動(傳統壓電傳感器精度約0.1 g),適用于高精度設備狀態監測;MEMS壓力傳感器量程覆蓋0~10 MPa,精度達±0.1% FS(滿量程),滿足液壓系統精準控制需求。
??多參數集成??:單顆PCB傳感器可集成多種敏感單元(如溫度+壓力+振動),實現多物理量同步采集。例如,汽車發動機監測傳感器可同時檢測缸內壓力(0~20 bar)、溫度(-40~150℃)及振動頻率(0~10 kHz),減少安裝空間并提升數據同步性。
??2. 高精度與低噪聲設計??
工業自動化對傳感器精度的要求日益嚴苛,尤其在精密制造(如半導體加工、光學元件生產)領域,微小誤差可能導致產品批量報廢。PCB傳感器通過以下技術提升精度:
??低噪聲信號調理電路??:采用斬波穩零放大器、Σ-Δ型ADC(模數轉換器)等技術,將噪聲水平降至0.1 μV級(傳統傳感器噪聲約1 μV),提升微弱信號檢測能力。例如,MEMS壓力傳感器的分辨率從0.1% FS提升至0.01% FS,可檢測0.001 MPa的壓力變化。
??溫度補償算法??:通過集成溫度傳感器(如PT100)和數字補償算法,消除環境溫度對測量結果的影響(溫度漂移從±0.5% FS/℃降至±0.05% FS/℃),確保全溫域(-40~125℃)下的高精度輸出。
??3. 智能化與邊緣計算??
傳統傳感器僅輸出原始電信號,需依賴上位機進行數據處理,實時性差且通信帶寬占用高。PCB傳感器正逐步集成微處理器(如ARM Cortex-M系列)和邊緣計算功能,實現數據本地化處理與智能決策:
??實時數據處理??:內置FPGA或DSP芯片,可對原始信號進行濾波(如卡爾曼濾波)、特征提取(如FFT頻譜分析)及異常檢測(如閾值報警),減少數據傳輸量(壓縮比達10:1)并提升響應速度(延遲<1 ms)。
??自診斷與自校準??:通過內置算法實時監測傳感器狀態(如零點漂移、靈敏度衰減),自動觸發校準程序(如溫度補償系數更新)或故障報警(如輸出信號異常時標記“失效”狀態),降低維護成本(預測性維護可減少30%停機時間)。
??4. 網絡化與協議兼容性??
工業物聯網(IIoT)要求傳感器具備聯網能力,實現設備間數據互通與遠程監控。PCB傳感器通過集成無線或有線通信模塊,支持多種工業協議:
??無線通信??:采用低功耗藍牙(BLE 5.0)、Wi-Fi 6或ZigBee技術,實現10~100 m范圍內的數據傳輸(功耗<10 mW),適用于移動設備(如AGV小車)或布線困難的場景(如旋轉機械監測)。
??有線通信??:支持工業以太網(如PROFINET、EtherCAT)和現場總線(如Modbus RTU/TCP、CANopen),通信速率達100 Mbps以上,滿足高實時性控制需求(如伺服電機閉環控制周期<1 ms)。
??協議轉換功能??:部分PCB傳感器集成協議網關功能,可兼容多種工業協議(如同時支持Modbus和PROFIBUS),簡化系統集成(減少網關設備數量,降低成本30%以上)。
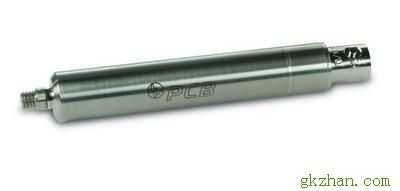
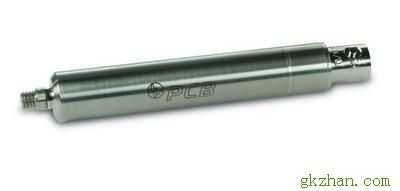
??二、PCB傳感器的功能拓展與應用深化??
??1. 狀態監測與預測性維護??
工業設備的突發故障可能導致產線停產甚至安全事故,PCB傳感器通過實時監測關鍵參數(如振動、溫度、電流),結合大數據分析實現預測性維護:
??振動監測??:MEMS加速度傳感器檢測設備軸承、齒輪箱的振動頻譜(頻率范圍0.1~10 kHz),通過頻域分析識別故障特征(如軸承內圈磨損對應1.2 kHz峰值),提前預警(故障發生前1~2周發出報警),避免非計劃停機(維護成本降低40%)。
??溫度監測??:薄膜鉑電阻(PT100)或熱電堆傳感器實時監測電機繞組、變壓器油溫,結合溫升速率分析(如ΔT>5℃/min提示過載),防止設備過熱損壞(故障率下降50%)。
??2. 精密制造與過程控制??
在半導體加工、3D打印等高精度制造領域,PCB傳感器為工藝參數控制提供關鍵數據支撐:
??壓力控制??:電容式壓力傳感器檢測化學氣相沉積(CVD)設備的反應腔壓力(精度±0.01% FS),確保薄膜沉積厚度均勻性(偏差<±1 nm);
??位移監測??:LVDT(線性可變差動變壓器)或電容式位移傳感器實時測量數控機床刀具的位置(分辨率0.001 mm),提升加工精度(誤差<±2 μm)。
??3. 能源管理與環保監測??
PCB傳感器在能源效率提升和污染排放控制中發揮重要作用:
??能耗監測??:電流傳感器(如霍爾效應傳感器)檢測電機、變頻器的實時電流(精度±0.5%),結合功率分析算法計算能耗(單位:kWh),優化設備運行策略(節能10%~20%);
??氣體泄漏檢測??:MEMS氣體傳感器(如MQ-135檢測VOCs、NO?傳感器)監測化工管道、儲罐的氣體濃度(檢測限ppb級),預防爆炸或中毒事故(響應時間<1 s)。
??三、行業應用案例與市場前景??
??1. 汽車制造:從傳統燃油車到新能源汽車??
??燃油車??:PCB壓力傳感器用于發動機燃油噴射系統(量程0~5 MPa,精度±0.5%),提升燃燒效率(油耗降低5%);溫度傳感器監測變速箱油溫(-40~150℃),防止過熱損壞。
??新能源汽車??:電流傳感器檢測電池包充放電電流(精度±0.1%),確保電池管理系統(BMS)的安全運行;加速度傳感器監測碰撞時的減速度(閾值200 m/s²),觸發安全氣囊(響應時間<20 ms)。
??2. 電子制造:半導體與PCB生產??
??晶圓制造??:MEMS壓力傳感器控制化學機械拋光(CMP)設備的拋光頭壓力(精度±0.01% FS),確保晶圓表面平整度(偏差<±0.1 nm);
??PCB組裝??:視覺傳感器(集成于PCB的CMOS攝像頭)檢測焊點質量(分辨率20 μm),替代人工目檢(效率提升3倍,誤檢率<0.1%)。
??3. 能源電力:風電與電網監測??
??風力發電機??:振動傳感器監測主軸、齒輪箱的運行狀態(頻率范圍0.1~1 kHz),預測軸承故障(提前2周報警);風速傳感器(超聲波原理)實時測量風速(精度±0.5 m/s),優化葉片角度控制(發電效率提升8%)。
??智能電網??:電流傳感器監測輸電線路的負荷電流(精度±0.2%),結合物聯網平臺實現故障定位(定位誤差<100 m),縮短停電時間(平均修復時間MTTR<30 min)。
??四、挑戰與未來發展方向??
??1. 當前挑戰??
??可靠性問題??:工業環境中的高溫(>150℃)、高濕(RH>95%)、強電磁干擾(EMI)可能導致PCB傳感器性能下降(如MEMS芯片失效);
??標準化不足??:不同廠商的傳感器接口、通信協議差異大,增加系統集成難度(如需定制轉接板);
??成本壓力??:PCB傳感器(如集成AI算法的智能傳感器)單價>1000元,限制中小企業的普及。
??2. 未來發展方向??
??新材料與新工藝??:采用氮化鋁(AlN)基板替代傳統FR-4 PCB,提升耐高溫性能(工作溫度>200℃);應用3D打印技術實現傳感器微結構一體化成型,降低成本(降幅達30%)。
??AI與邊緣智能融合??:集成深度學習模型(如卷積神經網絡CNN),實現復雜故障模式識別(如齒輪箱裂紋擴展預測);邊緣節點部署聯邦學習算法,在保護數據隱私的同時優化全局模型精度。
??綠色低碳設計??:開發低功耗傳感器(靜態電流<1 μA),結合能量收集技術(如振動能、太陽能供電),實現自維持運行(無需外部電源)。
??五、結論??
PCB傳感器作為工業自動化控制的核心感知單元,正通過微型化、智能化、網絡化的技術革新,推動工業設備從“功能型”向“智能型”升級。未來,隨著新材料、AI算法及物聯網技術的深度融合,PCB傳感器將在智能制造、綠色能源等領域釋放更大潛力,為工業高質量發展提供更精準、高效的數據支撐。